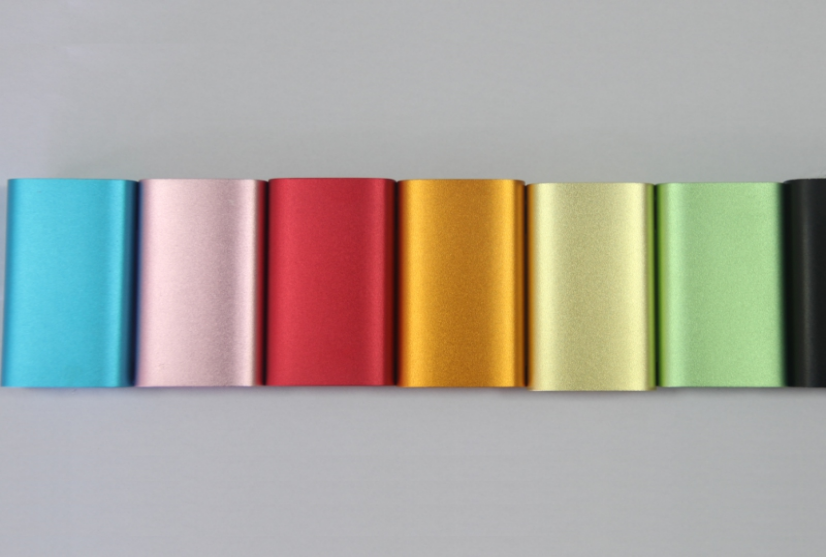
In the production and application of aluminum alloy parts, surface treatment is a crucial step. It not only enhances the appearance quality of the parts but also improves their performance and extends their service life. CS Molding has accumulated years of experience in the field of aluminum alloy parts processing and has an in-depth understanding and practice of various surface treatment processes. However, with numerous surface treatment technologies available, how to select the most suitable one for aluminum alloy parts remains a problem for many enterprises and practitioners.
1.Choose Based on Usage Scenarios
If the parts are used outdoors and exposed to wind, sun, rain, and snow for a long time, corrosion resistance becomes the primary consideration. Anodizing performs excellently in this regard. It can form a dense oxide film on the surface of aluminum alloys, effectively blocking the intrusion of external corrosive media and keeping the parts in good condition in outdoor environments. CS Molding once produced aluminum alloy shell parts for an outdoor lighting enterprise. Since the lamps needed to work outdoors for a long time, we recommended anodizing. After two years of use feedback, these parts still showed no obvious signs of corrosion. Outdoor aluminum alloy doors, windows, railings, etc., mostly adopt this treatment method.
If the parts are used inside electronic equipment, which have high requirements for insulation performance and surface flatness, chemical conversion coating treatment may be a good choice. This treatment can form a thin chemical film on the surface of the parts, which not only has certain insulation properties but also ensures a flat and smooth surface, meeting the precision requirements of electronic equipment for parts. CS Molding used chemical conversion coating treatment for the internal connectors produced for an electronic instrument company, which well met the insulation and precision assembly requirements of the instrument.
Advantages:
- Strong adhesion
- Economical and efficient
- Good anti-corrosion performance
Use: drones, electrical cabinets, automation equipment, smart homes, etc.
2. Select According to Required Performance
If it is necessary to improve the hardness and wear resistance of the parts, hard anodizing is the ideal option. After this treatment, the hardness of the oxide film on the surface of aluminum alloy parts is greatly increased, enabling them to withstand large friction and wear. It is suitable for parts that often need to contact and move with each other, such as aluminum alloy components in mechanical transmission. CS Molding produced aluminum alloy transmission parts for a machinery manufacturing enterprise. After hard anodizing, the service life of these parts was more than three times longer than that of the untreated parts before.
For parts with decorative needs, electroplating can show its advantages. Electroplating can plate a layer of other metals, such as chromium and nickel, on the surface of aluminum alloys, making the parts present a bright and beautiful appearance, enhancing the overall texture and added value of the product. It is often used in some decorative aluminum alloy products, such as aluminum alloy decorative parts on furniture. CS Molding once processed aluminum alloy decorative strips for a high-end furniture brand. Through electroplating, these decorative strips showed a mirror-like luster, which was well received by customers.
3. Consider Cost Factors
Different surface treatment processes have significant cost differences. Processes such as anodizing and electroplating are relatively complex and have higher costs; while chemical conversion coating treatment is simpler and has lower costs. CS Molding usually chooses chemical conversion coating treatment when processing small and medium batches of simple aluminum alloy bracket parts. While meeting the basic performance requirements, it helps customers effectively control costs. When choosing, it is necessary to select the most cost-effective treatment method based on the enterprise’s cost budget under the premise of meeting performance and usage requirements.
Use: Aluminum plates, automation equipment housings, consumer electronics, audio housings
4. Refer to Industry Solutions
You can also refer to the surface treatment schemes of similar products in the same industry, learn from their experiences and lessons, and then adjust and optimize according to the characteristics of your own products. CS Molding also often studies excellent cases in the same industry to continuously improve its own surface treatment schemes.
In summary, the selection of surface treatment methods for aluminum alloy parts requires consideration of usage scenarios, performance requirements, costs and other factors, and the most appropriate solution is selected through analysis and comparison. CS Molding has always adhered to this principle and insisted on using its rich experience to provide customers with high-quality aluminum alloy parts surface treatment services, providing strong guarantees for the quality and performance of your products.
For more information or to request a quote, contact us today.