Selecting the right mold system is crucial for efficient and high-quality injection molding production. Hot runner molds and cold runner molds are two commonly used options in the industry, each with its own advantages and considerations. This article aims to provide an in-depth comparison of these mold systems, highlighting their characteristics, benefits, and drawbacks.
Hot Runner Molds: Hot runner molds, also known as hot manifold molds, maintain a constant temperature in the runner system. These molds eliminate the need for a solidified sprue and runner system by heating the channels through which molten plastic flows from the injection molding machine nozzle to the mold cavities.
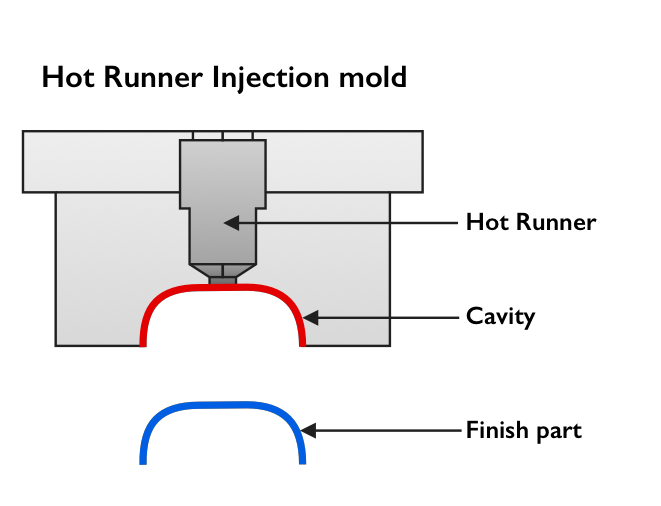
Advantages of Hot Runner Molds:
- Reduced Material Waste: Hot runner molds minimize material waste by eliminating the need for ejecting and discarding sprues and runners, resulting in cost savings and increased efficiency.
- Faster Cycle Times: The absence of cooling and solidification time for the runner system allows for faster cycle times, leading to improved productivity and higher production output.
- Improved Quality: Hot runner molds offer better control over the flow of molten plastic, reducing the likelihood of issues such as flow lines, weld lines, or gate blush. This results in improved part quality and consistency.
- Versatility: Hot runner systems accommodate multiple gates and complex part geometries, providing design flexibility suitable for a wide range of applications.
Advantages of Hot Runner Molds:
- Reduced Material Waste: Hot runner molds minimize material waste by eliminating the need for ejecting and discarding sprues and runners, resulting in cost savings and increased efficiency.
- Faster Cycle Times: The absence of cooling and solidification time for the runner system allows for faster cycle times, leading to improved productivity and higher production output.
- Improved Quality: Hot runner molds offer better control over the flow of molten plastic, reducing the likelihood of issues such as flow lines, weld lines, or gate blush. This results in improved part quality and consistency.
- Versatility: Hot runner systems accommodate multiple gates and complex part geometries, providing design flexibility suitable for a wide range of applications.
Considerations for Hot Runner Molds:
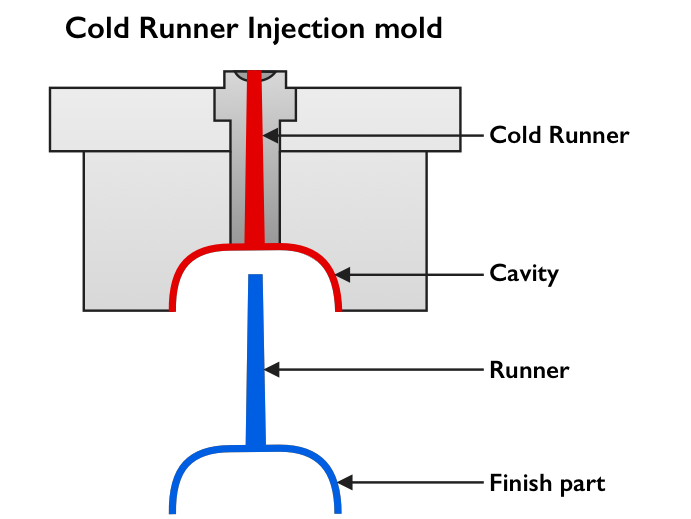
1.Higher Initial Cost: Hot runner molds require additional components and systems, making them more expensive upfront. However, the potential cost savings from reduced material waste and increased productivity can offset this initial investment in the long run
2.Maintenance and Complexity: Hot runner molds are more complex than cold runner molds, requiring regular maintenance and skilled technicians to troubleshoot and repair any issues with the heated systems.
Cold Runner Molds: Cold runner molds utilize unheated channels (runners) to deliver molten plastic to the mold cavities. The solidified sprue, runner, and gate system are ejected and discarded along with the part after each injection cycle.
Advantages of Cold Runner Molds:
- Lower Initial Cost: Cold runner molds are generally more affordable upfront as they do not involve additional heating components and systems.
- Simplicity and Maintenance: Cold runner molds are simpler in design and operation, making them easier to maintain and repair compared to hot runner molds.
- Suitable for Large Parts: Cold runner molds are well-suited for larger parts where the solidified runner material can be reclaimed and recycled without significant cost implications.
Lorem ipsum dolor sit amet, consectetur adipiscing elit. Ut elit tellus, luctus nec ullamcorper mattis, pulvinar dapibus leo.