Introduction
Plastic injection molding is a widely used manufacturing process for producing plastic parts. However, it is not without its challenges, and defects can occur during production. Understanding and addressing these defects is crucial to ensure high-quality finished products. In this comprehensive guide, we will explore the top five common plastic injection molding defects, along with effective solutions to overcome them. Additionally, we will discuss a few more defects and their respective remedies, providing you with valuable insights into optimizing your injection molding process.
Ⅰ.Top 5 Plastic Injection Molding Defects
1. Sink Marks
Sink marks are depressions or dents on the surface of a molded part caused by shrinkage during cooling. To minimize sink marks, you can try the following solutions:
- Increase the injection pressure: Higher pressure can help fill the mold cavity more completely, reducing the likelihood of sink marks.
- Adjust the gate location: Changing the gate location can influence the flow pattern, ensuring more even filling and reducing sink marks.
- Increase cooling time: Allowing the part to cool for a longer period can reduce the chance of sink marks appearing.
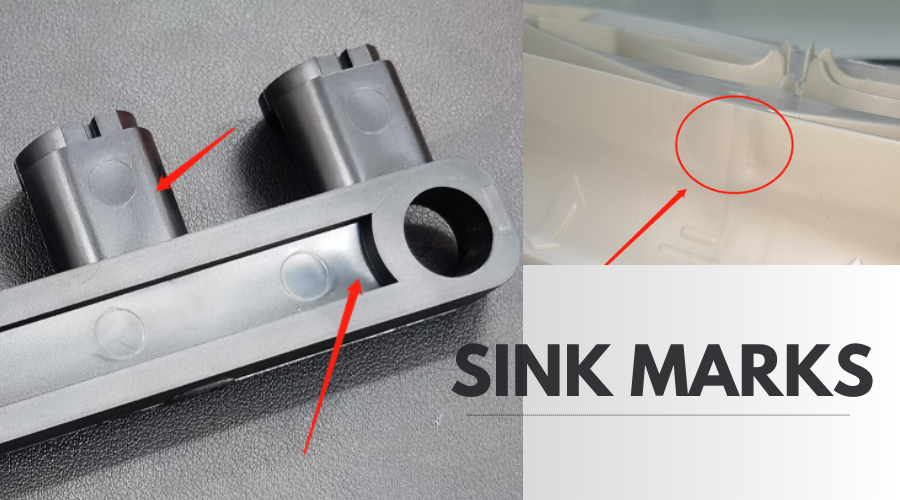
2. Warping
Warping refers to the deformation or twisting of a molded part after it has cooled down. To address this issue, you can consider the following actions:
- Optimize the mold design: Ensure that the mold is properly designed with appropriate cooling channels to promote uniform cooling and minimize warping.
- Adjust the melt temperature: Lowering the melt temperature can help reduce internal stress in the part, minimizing the potential for warping.
- Use a different material: Some materials have a lower tendency to warp compared to others. Experimenting with different materials may help alleviate the problem.
3. Flash
Flash occurs when excess material seeps out between the mold halves. Resulting in thin, unwanted protrusions along the edges of the part. To prevent flash, you can try the following remedies:
- Increase clamping force: A higher clamping force can help maintain proper mold closure and prevent material from escaping.
- Check for mold damage or wear: Inspect the mold for any damage or wear that might cause gaps between the mold halves, allowing the material to escape.
- Adjust process parameters: Modifying injection speed, pressure, or temperature can influence the flow of material and reduce the occurrence of flash.
4. Short Shot
A short shot happens when the material does not completely fill the mold cavity, resulting in an incomplete or undersized part. To overcome this issue, consider the following solutions:
- Increase injection pressure and speed: Higher pressure and faster injection can improve material flow and fill the mold more effectively.
- Check for obstruction or blockages: Ensure that there are no blockages or restrictions in the mold, such as partially closed vents, that could hinder material flow.
- Increase melt temperature: Raising the melt temperature can improve the material’s flow characteristics, allowing it to reach all areas of the mold cavity.

5. Void or Air Trap
Voids are air pockets or trapped gases that result in empty spaces or bubbles within the molded part. To reduce or eliminate voids, you can try the following approaches:
- Optimize venting: Ensure that the mold has proper venting to allow air and gases to escape during the injection process.
- Increase mold temperature: Raising the mold temperature can help reduce the likelihood of air getting trapped within the material.
- Adjust injection speed and pressure: Slower injection speeds and higher pressures can improve material flow and minimize the chances of air getting trapped.
Ⅱ. Additional Plastic Injection Molding Defects and Solutions
6. Weld Lines
Weld lines occur when two or more flow fronts meet and solidify, resulting in a visible line or mark on the surface of the part. To mitigate weld lines, you can consider the following actions:
- Adjust gate location: Changing the gate location can alter the flow pattern, allowing the melt fronts to merge in a less noticeable area.
- Increase melt temperature: Raising the melt temperature can improve material flow and minimize the appearance of weld lines.
- Optimize injection speed: Modifying the injection speed can influence the flow fronts’collision, reducing the visibility of weld lines.
7. Splay Marks
Splay marks are streaks or lines on the surface of the part caused by trapped moisture or volatile gases in the material. To address splay marks, you can try the following remedies:
- Dry the material: Ensure that the plastic material is adequately dried before injection molding to reduce the presence of moisture.
- Adjust melt temperature and residence time: Increasing the melt temperature and reducing the residence time can help remove trapped gases from the material before injection.
- Check for contamination: Contaminants, such as lubricants or other foreign substances, can contribute to splay marks. Ensure that the material and the injection molding environment are clean.
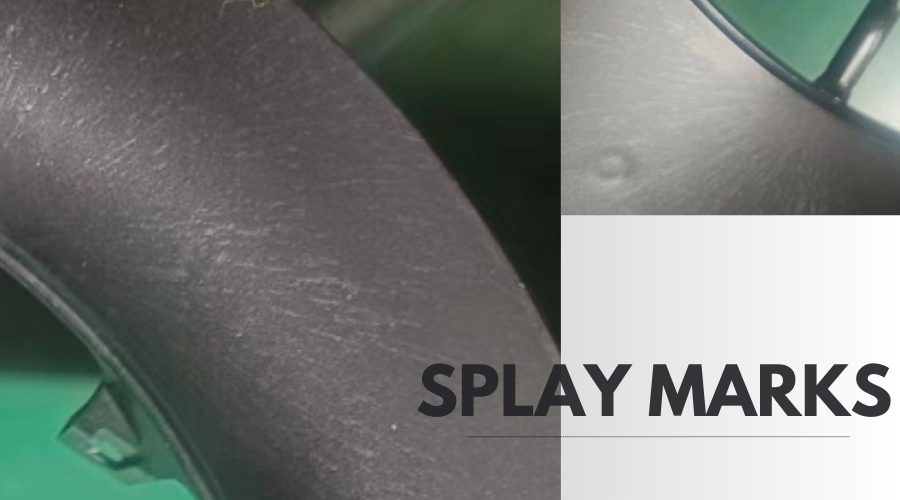
8. Jetting
Jetting refers to the phenomenon where the molten plastic material streams into the mold cavity, resulting in a visible distortion or misalignment of features. To minimize jetting, you can try the following solutions:
- Increase injection speed: Higher injection speeds can help break up the molten material into smaller streams, reducing the chance of jetting.
- Modify gate design: Adjusting the gate design, such as using a wider gate or adding a gate sub-runner, can improve the flow pattern and minimize jetting.
- Optimize material viscosity: Choosing a material with lower viscosity or using additives to reduce viscosity can help alleviate jetting issues.
9. Burn Marks
Burn marks are discolorations or blackened areas on the surface of the part caused by excessive heat during the injection molding process. To prevent burn marks, you can consider the following actions:
- Reduce melt temperature: Lowering the melt temperature can help avoid overheating the material and reduce the likelihood of burn marks.
- Optimize cycle time: Ensure that the cooling time is sufficient to allow the part to solidify and cool before ejection, preventing prolonged exposure to excessive heat.
- Improve ventilation: Proper venting can help dissipate heat and prevent localized overheating, minimizing the risk of burn marks.
10. Delamination
Delamination occurs when layers of the molded part separate or peel apart. This defect is often associated with inadequate bonding between layers. To tackle delamination, you can try the following remedies:
- Adjust mold temperature: Increasing the mold temperature can enhance the bonding between layers and reduce the likelihood of delamination.
- Optimize injection speed and pressure: Modifying the injection speed and pressure can improve material flow and promote better bonding between layers.
- Ensure proper material compatibility: Some materials may have compatibility issues, leading to delamination. Make sure that the materials used are suitable for the desired bonding strength.
Conclusion
Plastic injection molding defects can significantly impact the quality and integrity of the final products. However, by understanding the common defects and their respective solutions, manufacturers can take proactive measures to optimize their processes. Whether it’s addressing sink marks, warping, flash, short shots, voids, or other defects like weld lines, splay marks, jetting, burn marks, or delamination, careful analysis, and systematic adjustments can lead to improved outcomes. By implementing the suggested remedies, manufacturers can enhance the efficiency, reliability, and overall quality of their plastic injection molding operations.